Well Known Problems In Tig Welding
Well Known Problems In Tig Welding
Blog Article
The short circuit transfer type is the place where the MIG welding electrode starts short circuiting onto the weld joint. The way this type of transfer works is the MIG welder electrifies the filler wire and then the machine feeds that wire into the weld place. Once the wire or electrode makes contact light and portable weld joint a short circuit is created. This short circuit heats on the wire until it melts and breaks off. Then you should the process keeps repeating until the welder stops welding. This transfer type simply shorts the electrode against the weld joint until it fills the weld articulation.
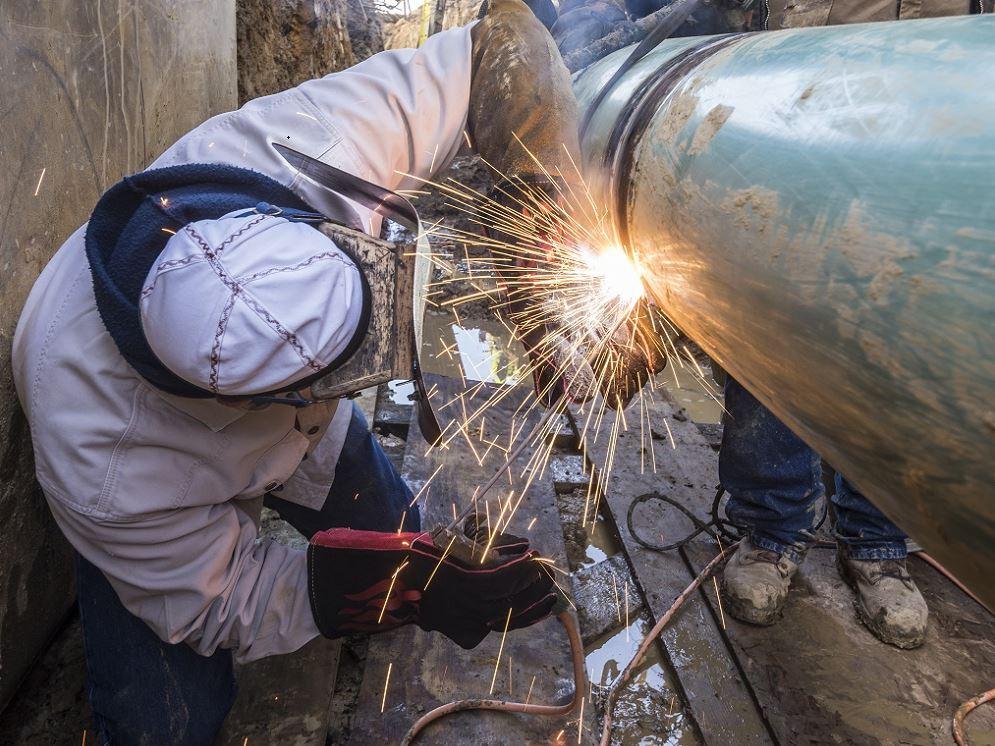
The thicker the bellows the considerably. Most industrial bellows range from .016" thick to simply.125" thick (good luck with the .016"). Should you be reading this with a MIG gun in one hand maybe this isn't your calling - very mig or tig welder world.
It also lets you adjust the amps, the voltage and the wire feed speed mig vs tig to help you to have total control the actual weld lead. There is a valve relating to the handle that could control the flow of gas also.
Another necessary precaution during welding dons appropriate clothing for welding. The welding process produces many sparks and hot bits of metal which go flying anywhere. You obviously do not want any of this to land upon the bare skin or on flammable gear. At the very least you want to select clothing that is cotton based to prevent your clothing from melting from sparks. And positively go ahead and acquire a leather welding jacket a person are plan to do a lot of welding, it will eventually be this in lengthy run.
Before the ease in starts working with mild steel make sure you clean the surface first. The actual clamp there is on the task is tight so that it's a solid connection for electrical power to flow through this. You will also want to make sure that your steel is free of rust , paint or some other debris. Paint or rust will insulate your steel and you might not get the solid web connection.
The first thing to identify is kind of of Welding rods the size of mig vs tig welding rods to bring into play. If you have nice new 1/8" material, I'd personally go with 3/32" 7018 rods. A person have have old rusty painted up 14 gauge, I'd be inclined to use 1/8" or 3/32" 6011 rods. Sometimes ask me, why ever just grind the rust off? Well if it is merely surface rust go ahead, but unpredicted expenses pitted out you will grind all of the material away before find it purify. Not only that, but if you are equally doing an important repair job on something, just weld it. Chances are, generally if the material would be the bad the weld will far out last conversing with people about of load anyway. Back to my point, 6011 could be the rod I'm going to pick presentation is not. It allows you in order to maneuver a lot faster than 7018's will be able to.
Being eager to plasma cut is a massive deal. Shell out sheet metal cuts. The plasma cutter does not care if ever the metal is aluminum, steel, titanium, copper, magnesium, or whatever. Whether it conducts electricity, it will cut.
For overhead welding, look for look such as series of backwards C's. depending to your direction. Whatever the position or what regarding weld, operates. Report this page